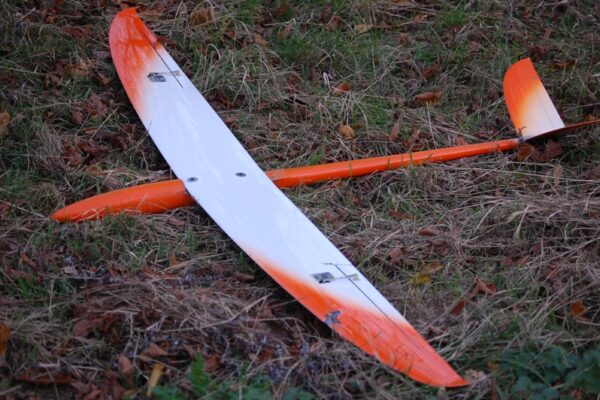
Da sich meine alte Ialomita im DS-Kreis zerlegt hat, war die neue Herausvorderung einen Flügel herzustellen, der nicht Festigkeits bedingt die Grenze im DS setzt.
Für die Holmauslegung wurde u.A. das Holmberechnungs-Programm von Christian Baron verwendet, welches man HIER herrunterladen kann.
Als Last wurde bei einer Geschwindigkeit von 140 m/s (=504 Km/h!) und einem Abfluggewicht 2,3 Kg ein CA von 1,15 angenommen. Das entspricht einem Lastvielfachen von 135 G! Das sollte halten und ergibt viele Rovings in einem Gurt… Immerhin 45m pro Schale! Der Holmgurt hat an der Wurzel eine Breite von 55 mm und läuft auf 10 mm aus. Die Abstufung der Rovings wurde bezüglich einer homogenen Krafteinleitung optimiert.
Laminieren der Oberschale
Als Erstes wird ein Roving in den Nasenleistenradius mit einlaminiert, somit stabilisiert man die Nasenleiste zusätzlich und verkleinert den Radius in den das Gewebe gelegt wird.Anschließend wird eine Lage 50 g/dm² Glasfaser laminiert. Hier wurde sie unter 45° verlegt, was aber nicht unbedingt nötig ist.
Als nächstes wurde eine komplette 200 g/dm² Kohlefaser-Leinen-Gewebe Lage und eine zweite Lage im Nasenbereich als D-Box laminiert. Beide müssen unter 45° verlegt werden.
Als Stützstoff wird 1 mm starkes Balsaholz verbaut. Die Aussparung für den Holm ist bereits eingeschnitten um ein geschlossenes Sandwich zu erhalten. Bei der Hartschalenfläche hat sich gezeigt, dass im Ruder kein Stützstoff benötig wird. Um das Sandwich zu schließen wird wieder eine komplette Lage 50 g/dm² Glasfaser über die gesamte Fläche laminiert.
Absaugfließ, Vakuumfolie und über Nacht absaugen
Laminieren der Unterschale
Die Unterschale wird gleich aufgebaut – einziger Unterschied: Es wird noch Abreißgewebe (rosa) nach dem Kohlefasergewebe als Schanierband mit einlaminiert. Bei diesem Flügel werden alle Ruder auf der Unterseite angeschlagen.
Die Unterschale fertig fürs Vakuum
Servosposition / Holmgurt herstellen
Wenn beide Seiten ausgehärtet sind, werden die Ausschnitte für die QR u. WK Servos mit einem Stechbeitel aus dem Stützstoff ausgeschnitten. Später wird das Sandwich mit Gewebe wieder verschlossen.
Wickeln des Holmgurtes: Ensprechend der Abstufung wurden Nägel in eine Leiste geschlagen, um die, jeweils die entsprechenden Windungen gewickelt werden.Eine Strichliste ist bei dieser Menge von Vorteil!
Wir haben den Holgurt pro Schale in zwei Teile geteilt um ihn besser tränken zu können.Bei diesen Mengen wären mehre Teile ratsam – oder direkt die geträngte Fasern aufwickeln.
Einlegen des Rovings. Um ein verrutschen zu verhindern wurde der Bereich verkastet.Wobei sich das Verkasten auch nicht optimal herausgestellt hat. Die Servoausschnitte auf der Oberschale wurden mit Glasfaser überlaminiert…
… auf der Unterseite (hier werden die Servos befestigt) mit Kohlefaser. So ist das Sandwich wieder verschlossen und für die Servos ist eine steifere Auflage und mehr Bauhöhe vorhanden.
Die Formhäften wurden wieder im Vakuum abgesaugt um die Gurte zu pressen.
Holmsteg / Zusammenfügen
Nach dem Aushärten wurden – in Frischhaltefolie eingewickelte – Knetebällchen auf die Stegpositionen gelegt und die Form geschlossen. So konnte nach dem Öffnen die Bauhöhe der Stege an den Bällchen gemessen werden.
Die Form des Holmsteges wurde einteilig aus 6+3mm Depron hergestellt und die Höhe des Steges entsprechend der Knete geschliffen.
Anschließend wurde der Steg in Streifen geschnitten, so breit, dass die Faser des später überzogenen Kohleschlauch unter 45° liegt. Der Steg im Flügel vor dem QR besteht auch aus überzogenem Depron, im Ruder liegen überzogene Strohalme.
Um ein verrutschen der Stege beim schließen der Form zu verhindern, wurden kleine Depron Dreiecke in die Form geklebt.
Um einen besseren Verbund zu erlangen, wurden alle Stellen die mit Mumpe / Stege in Berührung kommen mit Harz eingestrichen.Damit Unebenheiten vom Gurt ausgeglichen werden, wurde dieser mit Mumpe (wenig Baumwollflocken + mehr Microballons) eingestrichen
Positionierung der getränkten Stege.Anschließend wurde an Nasen- und Enleiste eine Raupe/ Wullst mit mehr Baumwollflockenanteil gelegt.Dann wurde die Form Verschlossen.
Öffnen der Flügelform
Der Schock beim Öffnen der Form: Es ist viel Farbe von der Oberschale in der Form hängengeblieben, ließ sich aber einfach aus der Form lösen, …
… viel mehr war kein Verbund zwischen Laminat und Farbe vorhanden und konnte auf der ganzen Oberseite einfach mit dem Fingernagel abgekratz werden.Mehr zu dem Problem wurde im RC-N ausgeführt. (Link)Die Unterseite war einwandfrei in Orndung.
Hier das Ergebnis der Oberschale, nachdem sie vollständig abgeschliffen, gefillert und neu lackiert wurde.Gewicht des Flügel: 992g
Ruderausschnitte / Anlenkung der Querruder
Nachdem die Flächenkonturen an Nasen und Endleiste beschliffen sind, wird die Position des Ruders auf dem Flügel angezeichnet. Für die Führung der Säge wird ein Stahllineal entlang der Schnittlinie positioniert (Am besten Malertape auf unterseite vom Lineal aufkleben, so verhindert man ein Verkratzen)
Die Schnitte werden mit einer Schwingsäge ausgeführt.
Auf der Achse, wo das Ruder angeschlagen werden soll, wird auch mit der Schwingsäge ohne Druck die Kohleschicht durchgesägt, bis man das Abreißgewebe rosa durchschimmern sieht…
… Der Rest wird durch bewegen des Ruders “freigebrochen”Auf dem Bild sieht man auch gut, dass mit Mumpe im Bereich der Schnittkante das Ruder (beim Zusammenfügen) “verkastet” wurde.
Servoschacht ausgeschnitten und löten des Kabelbaums
Der Kabelbaum wird am Flügel-/ Rumpfübergang mit einem Multiplexstecker getrennt. Die Lötstellen werden noch mit Heißkleber isoliert/versiegelt. So erhält man gleichzeitig eine Zugentlastung der Lötstelle.Leider konnte man nicht die orginale (F5B-Version) Ausbuchtung für den Stecker verwenden, da der Holm zu breit ist.
Die fertige Ruderanlenkung. Die Ruderhörner sind aus GfK Plattenmaterial und mit UHU Endfest eingeklebt.
Bau des V-Leitwerks
Leider sind mir die Bilder abhanden gekommen, es wurde aber auch mit 50g/dm² GfK diagonal, dann 200g/dm² CfK diagonal, 1mm Balsa Stützstoff und wieder 50g/dm² GfK diagonal, sowie einigen Rovings als Holm aufgebaut.
Der fertige Flieger
Als Rumpf habe ich einen Opusrumpf genommen. Hier wurde die Flächenauflage mit Spachtel angepasst. Das Leitwerk wurde mit CfK Schnitzel angeklebt und später mit einer 90g/dm² CfK Gewebe verstärkt.
Das Abfluggewicht liegt bei 1700g und kann bis 3000g aufbalastiert werden.
Das Flugverhalten vom Modell ist trotz der schweren Fläche recht agil und zugleich sehr neutral. Leider habe ich feststellen müssen, dass der Flieger für wirklich harten DS-Einsatz (viel Wind) etwas zu klein ist. Er wird trotz hohem Gewicht in der Grenzschicht stark gebeutelt.
Hier noch ein Video von ihrem letzten DS-Einsatz bei Sturm Xynthia (ab 2:46min)…
Christoph